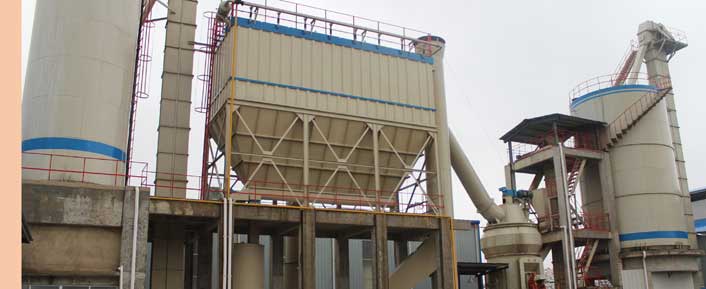


LM Vertical Grinding Mill
LM series grinding mill is my company in the relevant vertical grinding mill technology is more and more mature, technical advantages of vertical mill products increasingly prominent situation, actively learn from the successful experience of foreign countries, and constantly upgrading technology innovation through R & D team, launched with independent intellectual property rights of the vertical grinding mill products.
Detailed introduction
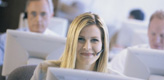
Online customer service
Welcome ! If you have any questions or suggestions about our products and services,please feel free to tell us anytime!
Detailed introduction
- 1. Energy saving environmental protection without pollution
Equipment, small vibration, low noise. The whole equipment sealing, the system works under negative pressure, no dust, clean environment, to meet the requirements of national environmental protection. - 2. Operation and maintenance more convenient
Equipped with PLC/DCS automatic control system, can realize remote control, simple operation. Through repairing cylinder, turning arm, replacing the roller sleeve, the lining board is convenient and fast, reduce downtime losses. - 3. Products stable quality high
The short residence time of material in the mill, easy to detect and control the product size and chemical composition, reduces repeated grinding, more stable product quality. No direct contact with the roller sleeve and a liner plate, iron content in the product and contained few, mechanical wear iron easy to remove, used for grinding white or transparent material, the whiteness of the product with high purity. Arranged for preventing roller sleeve and disc lining board in direct contact with the limit device, avoid destructive shock and vibration, therefore the quality and stability of the finished product to ensure significant.
Model | LM 130K |
LM 150K |
LM 170K |
LM 190K |
LM 220K |
LM 130M |
LM 150M |
LM 170M |
LM 190M |
LM 220M |
LM 130N |
LM 150N |
LM 170N |
LM 190N |
LM 220N |
|
---|---|---|---|---|---|---|---|---|---|---|---|---|---|---|---|---|
Wheel diameter(mm) | 1300 | 1500 | 1700 | 1900 | 2200 | 1300 | 1500 | 1700 | 1900 | 2200 | 1300 | 1500 | 1700 | 1900 | 2200 | |
Output (th) | 10-30 | 13-40 | 18-57 | 23-72 | 36-110 | 10-15 | 16-22 | 20-28 | 26-35 | 35-50 | 5-14 | 7-20 | 8-27 | 9-30 | 18-55 | |
Finish fineness | µm | 170-45 | 170-45 | 170-45 | 170-45 | 170-45 | 170-45 | 170-45 | 170-45 | 170-45 | 170-45 | |||||
Mesh | 80-325 | 80-325 | 80-325 | 80-325 | 80-325 | 80-325 | 80-325 | 80-325 | 80-325 | 80-325 | ||||||
Coal powder fineness (R0.08) | 5-20% | 5-20% | 5-20% | 5-20% | 5-20% | |||||||||||
Coal powder moisture (%) | <1% | <1% | <1% | <1% | <1% | |||||||||||
End product moisture (%) | ≤1% | ≤1% | ≤1% | ≤1% | ≤1% | ≤1% | ≤1% | ≤1% | ≤% | ≤1% | ||||||
Grinding material particle size D80 (mm) | <10 | <10 | <10 | <10 | <10 | <10 | <10 | <10 | <10 | <10 | <10 | <10 | <10 | <10 | <10 | |
Grinding material max feed size(mm) | <38 | <40 | <42 | <45 | <50 | <38 | <40 | <42 | <45 | <50 | <38 | <40 | <42 | <45 | <50 | |
Moisture of grinding material not to dry (%) | <4% | <4% | <4% | <4% | <4% | <4% | <4% | <4% | <4% | <4% | ||||||
Matieral moisture of into mill (%) | <15% | <15% | <15% | <15% | <15% | |||||||||||
Moisture of grinding material need to dry (%) | 4%-15% | 4%-15% | 4%-15% | 4%-15% | 4%-15% | 4%-15% | 4%-15% | 4%-15% | 4%-15% | 4%-15% | ||||||
Into mill air temperature (℃) | <350 | <350 | <350 | <350 | <350 | <350 | <350 | <350 | <350 | <350 | <350 | <350 | <350 | <350 | <350 | |
Out of the mill air temperature (℃) | 70-95 | 70-95 | 70-95 | 70-95 | 70-95 | 75-95 | 75-95 | 75-95 | 75-95 | 75-95 | 70-95 | 70-95 | 70-95 | 70-95 | 70-95 | |
Raw coal hardgrove grindability index (HGI) | >55 | >55 | >55 | >55 | >55 | |||||||||||
Main motor power (kw) | 200 | 280 | 400 | 500 | 800 | 185 | 250 | 315 | 400 | 500 | 200 | 280 | 400 | 500 | 800 | |
Contour dimension | Length (mm) | 5520 | 6550 | 7170 | 7580 | 8080 | 5520 | 6550 | 7170 | 7580 | 8080 | 5520 | 6550 | 7170 | 7580 | 8080 |
Width (mm) | 2500 | 3070 | 3460 | 3320 | 4660 | 2500 | 3070 | 3460 | 3320 | 6700 | 2500 | 3070 | 3460 | 3320 | 4660 | |
Height (mm) | 7060 | 7560 | 8300 | 8960 | 9020 | 7060 | 7560 | 8300 | 8960 | 9020 | 7060 | 7560 | 8300 | 8960 | 9020 |
[Feed size] : 38-55mm
[Capacity]: 10-50T / h
[Applications]: for cement, power, metallurgy, chemical, minerals and other materials milling industry. (More applications available online free consultation)
[Applicable materials] : cement, coal, feldspar, calcite, talc, fluorite, iron ore, copper, phosphate rock, graphite, quartz and slag.
Working principle
The main motor drives the disc through the speed reducer to rotate, and the hot air from the air inlet into the vertical mill body, disc material falling in the central through the feed port, under the action of centrifugal force, the material from the disc center to the edge of uniform movement, after grinding roller area the disc, by grinding roller compacted, large material crushed the fine-grained material is extruded, formed after the bed of interparticle breakage. The crushed materials continue to move to the edge of the grinding disc, until the wind was strong airflow at ring away, by the air flow with material, large granular material under the self gravity action again fell to the disc to smash, the remaining material with airflow into efficient dynamic separator in powder grading, in high dynamic separator the role of the leaves, do not meet the fineness requirement of material back to the millstones for grinding fineness, and meet the requirements of the material with gas flowing through the pipes into the pulse dust collector in the collection, through the discharging device is discharged into the finished product powder. The host within the mixed material such as iron hard abrasive debris along with the material moves to the edge of the grinding disc, due to its own weight and can not be blown up by the wind, to be installed in the millstone mill inferior at the bottom of the scraping plate scraping discharging port, discharging the external host.