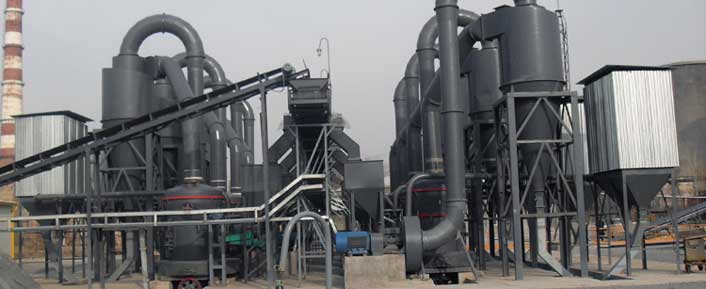


Vertical Roller Mill
Vertical roller mill is the most important product LM series vertical roller mill and LUM series vertical roller mill two vertical mill equipment, these two devices have different functions, but overall it has a production capacity strong, low operating cost advantages and can be used to produce cement, calcite, quartz, iron ore and many other industries including metallurgy, chemical industry, including the demand for raw materials, and the two devices have a lot of different models.
LM series vertical roller mill and LUM series of ultra-fine vertical roller mill both devices, there are many different beginning, for example, can produce material particle size, such as between the different models for each device in the shape, the production capacity terms are not the same, not the same as making the use of these devices are not the same, so when production can be to select the appropriate vertical roller mill equipment according to the needs of production engineering, which can better meet the production needs.
Detailed introduction
- 1. A high level of environmental protection
Small vibration, low noise. The whole equipment, sealing, and working under negative pressure, no dust, clean environment, higher than the national standard of environmental protection requirements. - 2. High grinding efficiency
The engine speed by frequency conversion, widely applicable to a variety of materials. Roller sleeve and a liner grinding curves with special design, form more easily than ordinary vertical grinding material layer, a grinding to the required product fineness. The use of mechanical and electronic dual limit protection device, effectively prevent the roller sleeve and the grinding disc lining board in direct contact, avoid destructive shock and vibration. - 3. Product quality
Using the principles of abrasive layer material in the mill grinding, short residence time, reduce duplication of milling, so products containing iron quantity few, the product whiteness and purity. The finished size less than 70% up to the powder content 2 m, realized 325 orders, low residue, and can increase two times the powder selecting, choose more fine grain size of the finished product. - 4. Good economic benefit
Multiple selection principle of powder machine, and each rotor adopts frequency control, a grinding fineness achieve finished at the selected range can be, without two times there is no inferior material sorting. Superfine grinding and long powder selecting principle, in the production of the same fineness grade products, compared with other mill, energy 30% ~ 50%, excellent economic benefit. - 5. Low cost input
Equipped with automatic control system, can realize remote control, simple operation. Using PLC/DCS automatic control of the grinding roller pressure control mode, the grinding pressure precision control, manual operation is not needed. The grinding roller and the grinding disc in the work without contact, and the grinding roller and the lining board is made of high quality material, less abrasion, long service life. Can turn out to the outside of the housing repair grinding roll, replacing the roller sleeve, liner is convenient, reduce the loss of shutdown. The grinding roller lubrication by using separate lubrication station, and the single roll grinding circuit adopts double pump pump suction and work mode, even if the grinding roll bearing fully lubrication and cooling, and can avoid the grinding roll bearing interior deposit more oil leak.
Model | LUM1125 | LUM1232 | LUM1436 |
---|---|---|---|
Wheel diameter(mm) | 1100 | 1200 | 1400 |
Capacity (t/h) | 5~12 | 7~16 | 8~18 |
Fineness 400~650Mesh | ~D97 | ~D97 | ~D97 |
Material Size(mm) | <10 | < 10 | <10 |
Moisture | <3% | <3% | <3% |
Main Motor Power(KW) | 250 | 315 | 355 |
Roller(set) | 3 | 3 | 3 |
Classifier Motor Power | 15 KWx5 | 15 KWx7 | 15 KWx7 |
[Feed size]: <10mm
[Capacity]: 5-18T / h
[Applications]: widely used in chemical industry, metallurgy, non-metallic mineral industries. (More online applications, please consult)
[Applicable materials]: Mohs hardness below 5, the density of 3.2 or less, compressive strength 150Mpa following, non-flammable mineral, non-corrosive materials brittle granular and powdered materials. Such as limestone, calcite, talc, barite, dolomite and other non-metallic minerals.
Working principle
The material through the spiral feeder falls on the disc center, main motor driving speed reducer by centrifugal force generated by the rotation of the driven disc, the material uniformly moving to the millstone around, when material passes through the disc roller region, by grinding roller of roller compacted, large material crushed, smaller particles were extruded forming material bed particles crushing. After being crushed materials continue to move to the edge of the grinding disc, is from the air flow into the inlet into the powder selecting machine classification, in the powder selecting machine blade under the effect of powder size does not meet the requirements into the disc re grinding, powder reached the standard with the airflow into the pulse dust collector was collected through the powder selecting machine. Powder collecting discharge is finished powder. Mixed iron and other impurities in the material, due to grinding and gravity itself, through the disc edge, cannot be the airflow away and fall into the inferior vena cava was scraping plate mill, sent to spit slag discharge port, the external host.